Technical
Metallurgical Services
At Rolled Alloys we offer metallurgical assistance as a complimentary service to our valued customers. We understand the importance of selecting the right materials, and our experienced and knowledgeable metallurgists are readily available to provide guidance and support.
We can also assist in performing failure analyses, providing sample coupons, and even perform lunch and learn presentations. With over 70 years of expertise in the specialty metals industry, our team of skilled metallurgists are equipped to help with any metallurgical-related scenario.
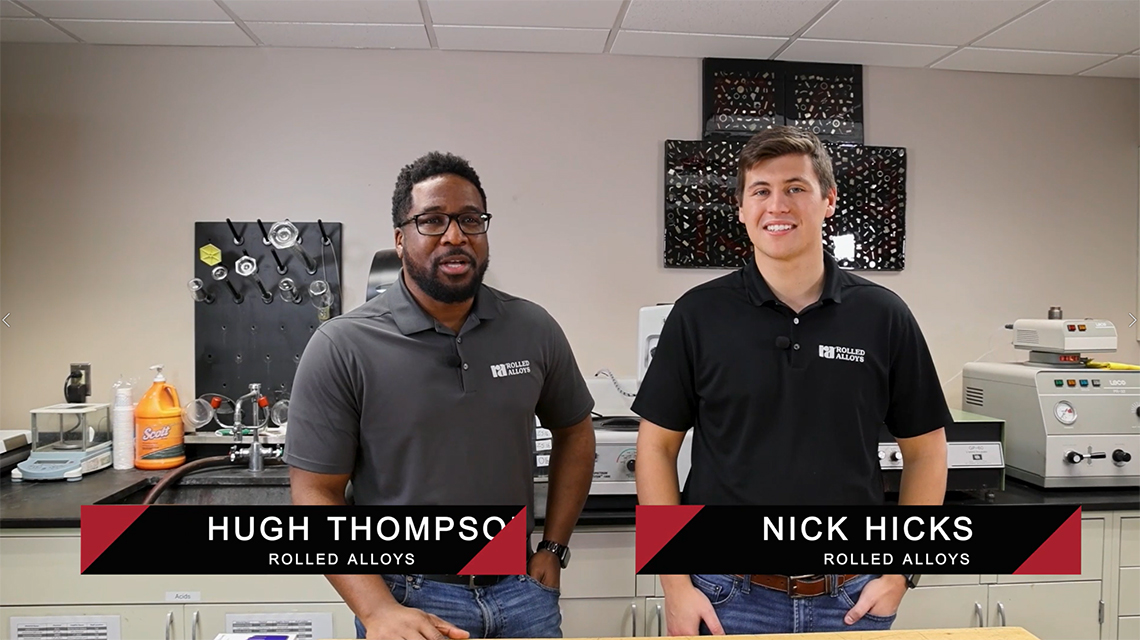
MEET THE TEAM
METALLURGICAL ASSISTANCE
LAB SERVICES
SAMPLE COUPONS
LUNCH & LEARNS
TECHNICAL RESOURCES
LATEST TECHNICAL BLOGS
High Temperature Strength – An Explanation of Creep and Rupture
Positive Material Identification (PMI)
The History and Uses of AL-6XN®
Bar Products: Specifications, Key Processes, and Common Confusions Explained
Chloride Stress Corrosion Cracking (CSCC) in Indoor Swimming Pools
What Are Raw Material Surcharges?
Quality of Microstructure of Duplex Stainless Steels
Flat Bar or Gauered Flat Bar from Plate
Metal Dusting
Manganese Substitution Grades of Stainless Steel
Plate Thickness Variations
Best Practices When Using Duplex Stainless Steels
Things to Know About PREN
Best Practices When Using Specialty Materials for SWRO Feed and Brine Reject Lines
Dual Certification
Determining Condition of Age-Hardenable Alloys
Understanding High-Temperature Distortion of Metals
Introduction to Heat Resistant Alloys
Sheet and Plate Flatness
Pipe Sizes and Tolerances
Machining Stainless Steel and Nickel Alloys
Ferrite Content in Austenitic Stainless Steels
Material Test Reports
Titanium Grades and Relative Properties
Stress Corrosion Cracking
Specialty Metals for Space Exploration
Inclusions in Specialty Alloys
How to Weld Duplex Stainless Steel
What is Sensitization and How to Avoid It?
Hydrogen Sulfide – NACE MR0175/ISO 15156 & NACE MR0103
Confused About Annealing and Heat Treating Terminology?
How Stainless Steel Rusts
Alloys and Acid Performance
Plasma or Laser Processing: To Cut or Not to Cut
Process vs. Process
Stop Corrosion Before It Starts
Frequently Asked Metallurgical Questions
Our team of metallurgical experts can assist in identifying alternative alloys for high-temperature and corrosive applications. Regarding alternative materials for critical applications (Aerospace, Defense, etc.), it is best to contact the OEM in charge of specifying materials to minimize potential liability. To contact a metallurgist, please click here.
To find out what filler metal you should use for a dissimilar metal joint, please visit our weld wire selector here.
Rolled Alloys has a full-service metallography lab that focuses on performing root cause analyses and metallography testing for customers. This service is free of charge to our customers.
If you are wondering which alloy is best suited for your application, we recommend that you contact our Metallurgical Services Team. They can provide valuable assistance if you can provide them with details of your application, such as metal temperature and process environment makeup.
To view machinability guidelines of specific alloys, please click here.
Click here to view machinability guidelines.
Martensitic stainless steels (410, 440C, 420, 416) and precipitation hardenable stainless steels (17-4, 15-5, 13-8, A-286) can be hardened by heat treatment. These are the only two classes of stainless steel that can be hardened by heat treatment. To understand heat treatment terminology better, please read our “Confused About Annealing and Heat Treating Terminology” blog.
The PREN is a calculated number based on an alloy’s chemical composition and is used to assess the resistance of stainless steels and nickel alloys to pitting corrosion, most typically chloride pitting. The higher the PREN, the better an alloy resists pitting corrosion. Alloys with higher PREN values are generally more suitable for aggressive environments. To read more about the PREN or to calculate the PREN of an alloy, please use our PREN Calculator.
MIG (Metal Inert Gas) welding, also known as GMAW (Gas Metal Arc Welding), is always done with spooled wire, usually 0.035″ or 0.045″, rarely 0.062″. TIG (Tungsten Inert Gas) welding, also known as GTAW (Gas Tungsten Arc Welding), is generally done with 36″ straight lengths of bare wire. Automatic TIG machines may use spooled wire, but 36″ lengths are only used for manual TIG. Electrodes are used for “stick welding”. They are typically 14″ lengths of wire, coated with a gray flux over all but the last 1-1/2 to 2″. Read More