Share:
Quote, Buy, Track!
We make it easy to get instant pricing and purchase your metal at the click of a button. Track your order progress, get notified when it ships, and follow your shipment online until it’s delivered. It’s that easy!
The basic 300 series stainless steels like 304/304L and 316/316L have an austenitic microstructure and are non-magnetic. In the annealed condition, they are essentially free of ferrite, which is magnetic.
Cast products of these alloys typically have some ferrite present. These alloys also form some ferrite when they are cold-worked or work-hardened. In both cases, the products will show a magnetic tendency. Ferrite can be detrimental to corrosion resistance in some environments. There are also applications where magnetic characteristics interfere with a product’s performance.
The ferrite content of a cast alloy can be controlled through alloy composition. Carbon, nitrogen, nickel, and manganese are strong austenite formers, and increasing their content in the alloy will reduce the tendency for ferrite formation. There are several different methods of predicting ferrite content, one of the more common is by utilizing the DeLong diagram. Ferrite reduces the tendency for the steel to solidification crack during cooling. It is common for 304 castings (CF8) to contain 8-20% ferrite. The cast ingot composition of wrought 304/304L stainless is also balanced to have 1-6% ferrite since this reduces the chance of cracking during forging or hot working.
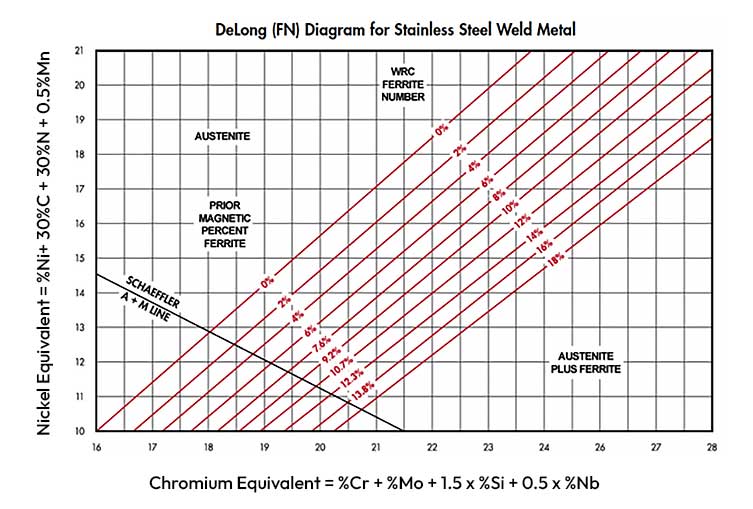
Solution annealing will dissolve most of the ferrite retained from ingot solidification. Because cast products are balanced to have a higher amount of ferrite, annealing will not transform all of it into austenite. However, little or no ferrite will remain in an annealed wrought product.
The DeLong diagram also predicts the amount of ferrite likely to be present in a weld deposit made from the wrought product. Plotting the composition of the wrought plate or bar product will indicate how much ferrite might be present if the material were re-melted (i.e., welding). Still, it is not a valid indicator of the ferrite content in the annealed product. Ferrite content in the actual product can be determined through laborious metallographic examination or by using sensitive magnetic instruments in a laboratory setting (magnetic permeability). However, in most cases, comparative calibrated magnets can establish an approximate ferrite content within 0.5 – 1%. Standard annealed 304/304L, 316/316L, 309, and 310 testing tends to yield 2% or less values. Often, ferrite contents are less than 0.5%.
It should also be noted that the matching filler metals used to join these alloys will also have higher ferrite contents. This is a precaution against solidification cracking during welding.
Depending on the alloy, the ferrite contents in the weld deposits will be between 5 – 10% ferrite. If ferrite-free welds are required, a higher nickel alloy filler should be selected, such as Alloy 20 (ER320LR) or Alloy 625 (ERNiCrMo-3).
Please contact the Rolled Alloys Metallurgical Services group at 1-800-521-0332 or submit your questions below.
Buy Online Anytime
Our dashboard makes it even easier to shop online anytime from anywhere. Quote, buy, and track 24 hours a day.
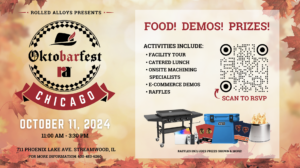
Chicago Oktobarfest 2024
Join us for food, demo’s and prizes on October 11th from 11 a.m to 3:30 p.m at 711 Phoenix Lake Ave, Streamwood, Illinois.
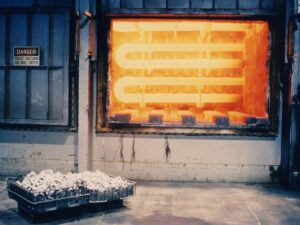
High Temperature Strength – An Explanation of Creep and Rupture
High Temperature Strength – An Explanation of Creep and Rupture Back To All Articles Share: More Articles Quote, Buy, Track! We make it easy to
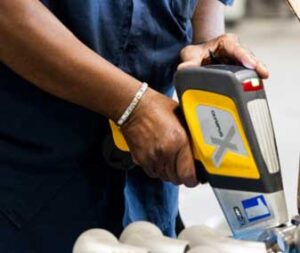
Positive Material Identification (PMI)
Positive Material Identification (PMI) Back To All Articles Share: More Articles Quote, Buy, Track! We make it easy to get instant pricing and purchase your
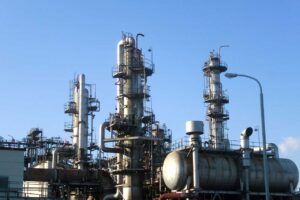
The History and Uses of AL-6XN®
The History and Uses of AL-6XN® Back To All Articles Share: More Articles Quote, Buy, Track! We make it easy to get instant pricing and
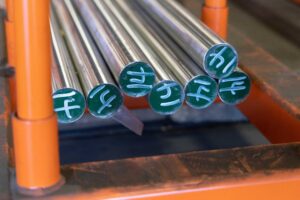
Bar Products: Specifications, Key Processes, and Common Confusions Explained
Bar Products: Specifications, Key Processes, and Common Confusions Explained Back To All Articles Share: More Articles Quote, Buy, Track! We make it easy to get
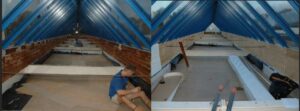
Chloride Stress Corrosion Cracking (CSCC) in Indoor Swimming Pools
Explore the causes and solutions for chloride stress corrosion cracking (CSCC) in 300 series stainless steels used in indoor swimming pool environments.